MTU Aero Engines - Product & Field Support
The Product and Field Support application makes field experience on engine components available. It coordinates the planning, execution and monitoring of maintenance requests and repair developments via workflows.
The task
A so-called “field inquiry” reaches MTU when a customer identifies a problem with one of the engines that he cannot solve on his own after consulting one of the maintenance manuals. The specific question is: Does the engine have to be disassembled or can it be repaired on site?
In such a case, Lufthansa, for example, contacts the OEM – e.g. Pratt & Whitney – and reports the anomaly on the engine. The OEM next checks who is responsible for a particular component or module on the engine – and then passes the inquiry on to MTU if it is affected. This happens more often than you might think: “We receive several inquiries in the various programs every day,” says the responsible engineering department. Such inquiries happen especially in the younger engine programs, such as the geared turbofan engine (GTF). MTU uses them to gather empirical data in order to optimize the product for different operating conditions. Coordinating the relevant processes is a complex task. The evaluations must be structured, efficient, comprehensible and interdisciplinary.
The benefits
Due to MTU’s specific processes, the choice of a suitable IT system platform proved to be challenging. After weighing up a wide range of criteria, the final choice was made in favor of the then relatively new development platform cplace, which is well suited to centralized data collection and collaboration.
Since the end of August 2020, MTU now has a tool that makes the flow of information in field requests transparent and supports project management in the process: the Product and Field Support application in cplace. It is a milestone in project management in the maintenance and support area. The application guarantees users standardized, digital project and workflow management in the planning, execution and monitoring of store inquiries and repair developments at MTU’s sites in the U.S., Munich and Rzeszów.
The tool meets the MTU experts’ requirement to systematically and structurally record all experience gained in the field and then make it evaluable. It also supports process and project management in the development of repairs and inspections, as well as their approval process vis-à-vis aviation authorities.
The services of 4Soft
MTU commissioned 4Soft to design and develop the Product & Field Support application. In an initial project phase, a proof-of-concept was created in a short time on the basis of the cplace platform from 4Soft partner collaboration Factory AG, which demonstrated the potential of the application and the platform. In the agile development project that followed, 4Soft then advanced the application sprint by sprint, built it out based on user feedback, and finally put it into operation.
“We experienced 4Soft as a development partner at eye level. The development benefited greatly from the fact that 4Soft employees not only brought technical IT knowledge to the table, but also understood and scrutinized our processes and requirements in detail. The result is convincing and takes MTU a big step forward in the maintenance and support area,” says the responsible project manager.
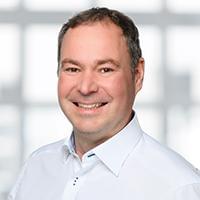