Smart Documentation
Industry 4.0 must not end at the factory gate
Many people initially associate the term Industry 4.0 with the digitization and networking of machines and production facilities to form intelligent factories - the smart factory. In our view, this notion is too narrow if we really want to take the “fourth industrial revolution” seriously. A holistic view of the industrial value chain is necessary, which includes not only the production of goods, but also their permanent support, maintenance and repair.
Industry in transition
Increasing digitization is not only changing the way production is carried out, but also the fundamental business models of companies. Today, customers are increasingly buying services instead of products: Airlines no longer buy engines but sign flight hour agreements, manufacturing companies buy holes instead of drills, and car manufacturers are transforming into mobility service providers, to name just a few examples.
Maintenance and repair, which used to be the customer’s responsibility, are now moving back to the manufacturer. On the one hand, this offers the opportunity to develop new business models, but on the other hand it also brings with it a change in the way companies look at the product life cycle. Efficient handling of the product after delivery is becoming a key competence. While maintenance and repair is often a revenue generator in the traditional product business, it is becoming a cost block in product-as-a-service business models.
But the products themselves are also undergoing change. New design processes and manufacturing methods (e.g., parametric models and 3D printing) make it possible to tailor industrial products individually to the customer - keyword “batch size 1”. The products themselves are becoming smarter and more networked. The proportion of electrical/electronic components and software in products is increasing.
More recently, supply chain bottlenecks and price pressure have been added as additional drivers for continuous product customization. Components can now no longer be selected and installed for one product generation, but must be used depending on availability.
The growing range of functions and the increasing number of variants and versions lead to a continuously increasing complexity of the products. People who are supposed to look after these products, for example in the area of maintenance and repair, are confronted with ever greater challenges. On the one hand, they have to take on increasingly demanding tasks; on the other hand, it is becoming more difficult for them to build up experiential knowledge, since no two copies are the same anymore.
Unfortunately, the requirements for the basic qualifications of employees cannot increase at the same rate as the complexity of the products grows. Factors such as the shortage of skilled workers, the global availability of products, and the different service models lead to a very heterogeneous qualification profile among people in operations and maintenance.
The concept of training employees in advance and then sending them into the field with all the necessary knowledge is also reaching its limits. Even the most qualified and experienced employee is no longer able to have everything “in his head”.
If such products are to be serviced efficiently and effectively in the future, interactive, targeted support for people during maintenance and operation is indispensable. The basis for this in each case is the provision of information that is precisely tailored to the respective need.
Status Quo
Systems theory says, “Only complexity can manage complexity.” Products are and will continue to become more complex, but what about the behavioral diversity and flexibility of product documentation in practice? Often, unfortunately, not so well.
Traditionally, development processes are designed to create a technical product specification for manufacturing. On this basis, the product documentation is then created with great effort in a (completely or partially) manual editing process.
In many cases, the state of the art is still paper documents or, if necessary, “digital paper” (PDF). Both variants are rather static by nature and often already outdated by the time they are printed. The digital PDF documentation is then viewed by employees on laptops or other mobile devices - if they do not print it out again in paper form for the sake of clarity.
Documentation in this form is neither up-to-date nor tailored to the individual product and the respective service or maintenance task. Its creation is time-consuming, error-prone and costly. The potential of “real” digitization remains untapped.
Solution approaches
We believe that the industrial revolution must also be accompanied by a revolution in the provision of information. Classic product documentation in the sense of static “documents” is no longer up to date and already fails to meet current and even more so future challenges.
According to our experience in various projects with customers, the following aspects are particularly important, which we summarize under the term “Smart Documentation”:
Documentation must be context-specific and tailored to the individual product copy: The flood of information must be reduced to what is really relevant for the user. Only information that is actually valid for the product in question is displayed; for example, equipment variants that are not available are filtered out or variable add-on parts are taken into account.
Documentation must be user-oriented: The views of the documentation must follow the respective work situation of the user (for example, in a “guided troubleshooting”). In addition, aspects such as the activities to be performed and the level of experience must also be taken into account.
Documentation must be interactive: Information provision must be interactive, with respect to both the user and the product. The user must be able to navigate interactively along his or her individual information needs. At the same time, real-time data (if possible) should be integrated as seamlessly as possible into the documentation (e.g., by comparing target/actual values).
If the digital world is linked with the real world, the resulting “augmented reality” opens up completely new possibilities. For example, interactive maintenance instructions can be created that are superimposed on the real device and illustrate the individual work steps of the worker, if necessary with additional support from an offsite expert consulted via the Internet.
With advanced digitalization, the one-way street of “product documentation” can thus become a value-creating highway.
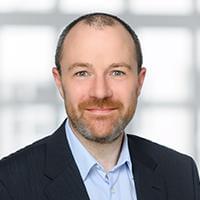